Understanding Plastic Injection Mold Making Service
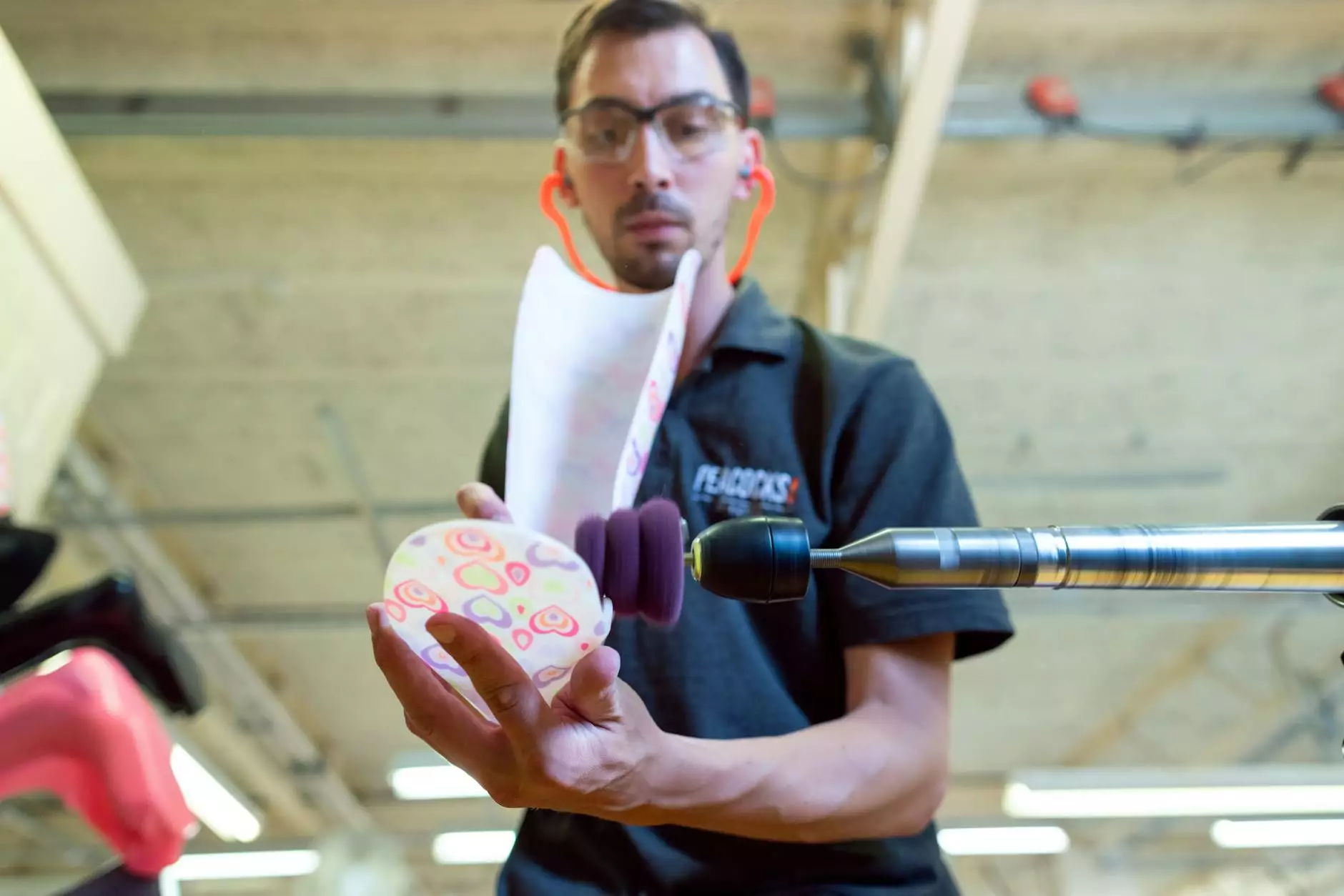
In the landscape of modern manufacturing, plastic injection mold making service stands as a cornerstone technique. This method transforms raw plastic materials into complex shapes and components, showcasing precision and efficiency. With a growing emphasis on efficiency, cost-effectiveness, and sustainability in production processes, understanding the nuances of injection molding is essential for any business in today’s competitive market.
What is Plastic Injection Molding?
Plastic injection molding involves the process of injecting molten plastic into a pre-designed mold. The mold is created to produce specific shapes and is crucial in ensuring the final product meets the required specifications. The process is versatile, accommodating a wide range of plastic types, which makes it an ideal choice for various industries.
The Steps in Plastic Injection Molding Process
- Designing the Mold: This is the initial step where the specifications of the product are defined. Engineers utilize CAD software to create a detailed design that meets the client's requirements.
- Creating the Mold: A mold is crafted from high-grade materials, typically steel or aluminum, ensuring durability and precision.
- Injection of Plastic: Once the mold is ready, molten plastic is injected into it under high pressure, filling every cavity perfectly.
- Cooling and Solidifying: The injected plastic is allowed to cool and solidify, taking the shape of the mold.
- Finishing: After cooling, the mold opens to eject the formed part, which may then undergo various finishing processes like trimming or painting.
Why Choose Plastic Injection Mold Making Service?
Businesses today benefit immensely from plastic injection mold making services due to numerous factors which include:
- High Efficiency: Once the mold is created, the production time for each piece is remarkably quick, allowing for rapid turnaround on large orders.
- Cost-Effectiveness: Although the initial mold creation can be expensive, the cost per unit decreases dramatically with larger production runs.
- Design Flexibility: Complex designs can be produced that would be difficult, if not impossible, to achieve with other manufacturing methods.
- High Precision: Injection molding allows for an exact and repeatable process which ensures that every part produced is identical, reducing waste and improving quality.
- Material Versatility: A wide array of plastics can be utilized, tailored to the specific requirements of the application, including those that offer durability, flexibility, or heat resistance.
Applications of Plastic Injection Molding
The applications of plastic injection mold making service span across various industries. Here are some notable sectors utilizing injection molded products:
1. Automotive Industry
Injection molded parts are extensively used in the automotive sector for components such as dashboards, interior trims, and exterior body parts. The ability to create lightweight yet durable parts is crucial for vehicle manufacturers.
2. Consumer Electronics
From housings to intricate internal parts, consumer electronics rely heavily on injection molding to produce components that meet both aesthetic and functional requirements.
3. Medical Devices
The medical industry benefits from the precision and cleanliness of injection molding, producing syringes, diagnostic devices, and various other tools while adhering to stringent safety standards.
4. Packaging
A plethora of packaging solutions, including bottles, containers, and lids, utilize injection molding for their strength and versatility.
5. Household Goods
Common household items like kitchen utensils, toys, and tools are produced using this method, showcasing the everyday relevance of injection molding.
How to Choose the Right Service Provider for Injection Mold Making?
Selecting the appropriate service provider for plastic injection mold making service is crucial for ensuring productivity and quality. Here are key factors to consider:
1. Experience and Expertise
Evaluate the provider’s experience in the industry. Companies with a long-standing presence typically have refined their processes and developed deep knowledge of various materials and production techniques.
2. Quality Assurance
Ensure they have robust quality control measures in place. This includes regular inspections and testing throughout the production process to adhere to industry standards.
3. Customization Capabilities
A key advantage of plastic injection molding is its customization potential. Choose a provider that can accommodate your specific design and material requirements.
4. Technological Advancements
Providers using the latest technologies and machinery can enhance the efficiency and accuracy of the mold-making process, providing a competitive edge.
5. Customer Service
Look for manufacturers that prioritize clear communication and customer relationships. A good provider will keep you informed throughout the project lifecycle, from design to delivery.
Sumiparts.us: Your Go-To for Plastic Injection Mold Making Service
At Sumiparts.us, we pride ourselves on providing comprehensive plastic injection mold making services tailored to meet diverse industrial demands. Our dedication to excellence spans various categories including Machining, Laser Cut, Welding, Vulcanized, and Industrial supplies.
Our Commitment to Quality
We understand that quality is non-negotiable in the manufacturing process. Our state-of-the-art equipment, combined with a skilled team of professionals, ensures that every part produced meets the highest industry standards.
Innovative Solutions
Innovation is key in staying competitive. At Sumiparts, we are constantly adapting to the latest advancements in manufacturing technology, ensuring that we provide efficient and cost-effective solutions for our clients.
Comprehensive Support
From initial design consultations to post-production services, our team is dedicated to supporting your projects at every stage. We work closely with our clients to understand their needs and deliver solutions that exceed expectations.
The Future of Plastic Injection Molding
The future of plastic injection mold making service is bright, with continuous advancements in technology paving the way for greater efficiency and creativity. Industries are increasingly recognizing the sustainability of using recyclable materials in injection molding, thereby enhancing environmental stewardship while maintaining product integrity.
Embracing Sustainability
As industries push toward sustainable practices, injection molding can contribute significantly through:
- Use of Recycled Materials: Many manufacturers are now capable of using recycled plastics in their production processes.
- Energy Efficiency: Modern machines are designed to consume less energy while maintaining high productivity.
- Reducing Waste: Improved precision in the molding process minimizes scrap material, contributing to overall waste reduction.
Conclusion
In conclusion, the plastic injection mold making service is an indispensable part of modern manufacturing, offering unparalleled efficiency, versatility, and precision. Whether you are in the automotive, electronics, or medical sector, understanding this process allows businesses to leverage its benefits effectively. At Sumiparts.us, we stand as your trusted partner in navigating these manufacturing challenges, providing top-tier solutions that help you rise above the competition.
For any inquiries about our services or to obtain a quote, please visit us at Sumiparts.us.