Use of Engineering Ceramics: Applications and Advantages
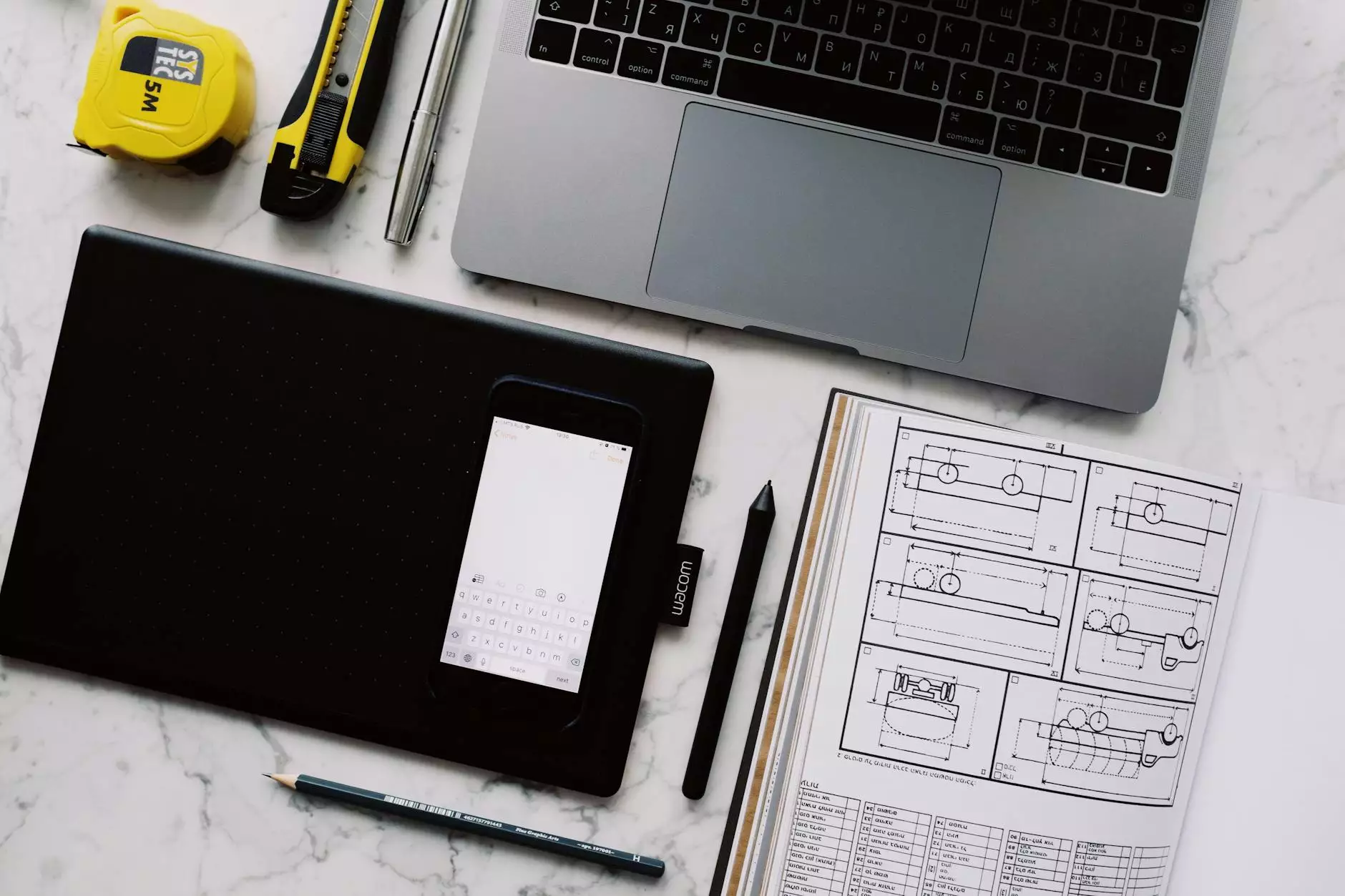
Introduction
Engineering ceramics, also known as advanced or fine ceramics, are a specialized group of materials that offer exceptional properties, making them highly valuable in various fields, from aerospace and automotive to electronics and biomedicine. With their unique combination of mechanical strength, thermal resistance, electrical conductivity, and corrosion resistance, engineering ceramics have revolutionized numerous industries by enabling groundbreaking advancements and enhancing overall performance.
Understanding Engineering Ceramics
Engineering ceramics are different from traditional ceramics due to their enhanced performance and precise manufacturing processes. These materials are typically composed of inorganic compounds, such as oxides, carbides, nitrides, or silicides, which are then formulated into precise compositions to obtain desired properties.
Applications in Aerospace and Defense
The aerospace and defense industries heavily rely on the use of engineering ceramics due to their exceptional strength, lightweight nature, and resistance to extreme temperatures and harsh environments. These materials are extensively used in the manufacturing of gas turbine engines, heat shields, rocket nozzles, and various structural components, where high-temperature performance, reliability, and structural integrity are critical.
Advancements in Automotive Engineering
In the automotive sector, engineering ceramics are utilized to improve fuel efficiency, reduce emissions, and enhance overall vehicle performance. Components like ceramic engine parts, catalytic converters, and brake systems benefit from the thermal resistance, wear resistance, and high melting points offered by engineering ceramics. These materials also contribute to weight reduction, leading to increased fuel economy.
Electronics and Semiconductor Industry
Engineering ceramics play a vital role in the electronics and semiconductor industry, where precision, reliability, and excellent electrical properties are essential. These materials are widely used in the production of microelectronic components, such as insulators, substrates, and electronic packaging. Their high dielectric strength and thermal stability make them particularly suitable for applications involving high frequencies, harsh environments, and miniaturization.
Medical and Dental Innovations
Engineering ceramics have paved the way for significant advancements in the medical and dental sectors. The biocompatibility, mechanical strength, and resistance to wear and corrosion make ceramics an ideal choice for various medical implants, prosthetics, dental crowns, and orthopedic applications. Furthermore, ceramics' ability to mimic the natural appearance of teeth contributes to their widespread use in cosmetic dentistry.
Manufacturing and Material Science
The manufacturing and material science fields benefit greatly from the utilization of engineering ceramics. The ability to withstand high temperatures, combined with excellent thermal shock resistance, makes ceramics suitable for foundry applications, welding, and metal casting. Additionally, ceramics find use in cutting tools due to their impressive hardness, wear resistance, and durability.
Properties of Engineering Ceramics
Engineering ceramics possess several key properties that set them apart from other materials:
- Mechanical Strength: Ceramics exhibit exceptional mechanical strength and hardness, making them suitable for load-bearing applications and offering resistance to wear and deformation.
- Thermal Resistance: Engineering ceramics have high melting points and excellent resistance to thermal shock, allowing them to withstand extreme temperatures and rapid temperature changes.
- Electrical Conductivity: Certain ceramics exhibit excellent electrical conductivity, making them valuable in electronic applications where electrical insulation or conductivity is required.
- Corrosion Resistance: Many engineering ceramics possess exceptional resistance to chemical corrosion, making them ideal for applications involving exposure to corrosive substances.
Manufacturing Processes of Engineering Ceramics
Engineering ceramics undergo intricate manufacturing processes to obtain their desired properties and precise shapes. Some common manufacturing methods include:
- Powder Compaction: Ceramic powders are carefully mixed, formed into shapes, and then subjected to high-pressure compaction, followed by heat treatment.
- Sintering: The compacted ceramics are heated to high temperatures in a controlled environment, causing the powders to fuse together, resulting in a solid, densely-packed structure.
- Hot Isostatic Pressing: In this process, ceramics are subjected to both high temperature and pressure simultaneously to further improve their density, strength, and eliminate any remaining porosity.
Conclusion
The use of engineering ceramics has revolutionized countless industries, enabling innovative solutions and driving technological advancements. With their exceptional mechanical, thermal, and electrical properties, engineering ceramics find applications in aerospace, automotive, electronics, medical, and manufacturing sectors. By understanding the unique properties and manufacturing processes of engineering ceramics, professionals and experts in the field can harness the full potential of these remarkable materials.