Understanding Injection Molding Manufacturing
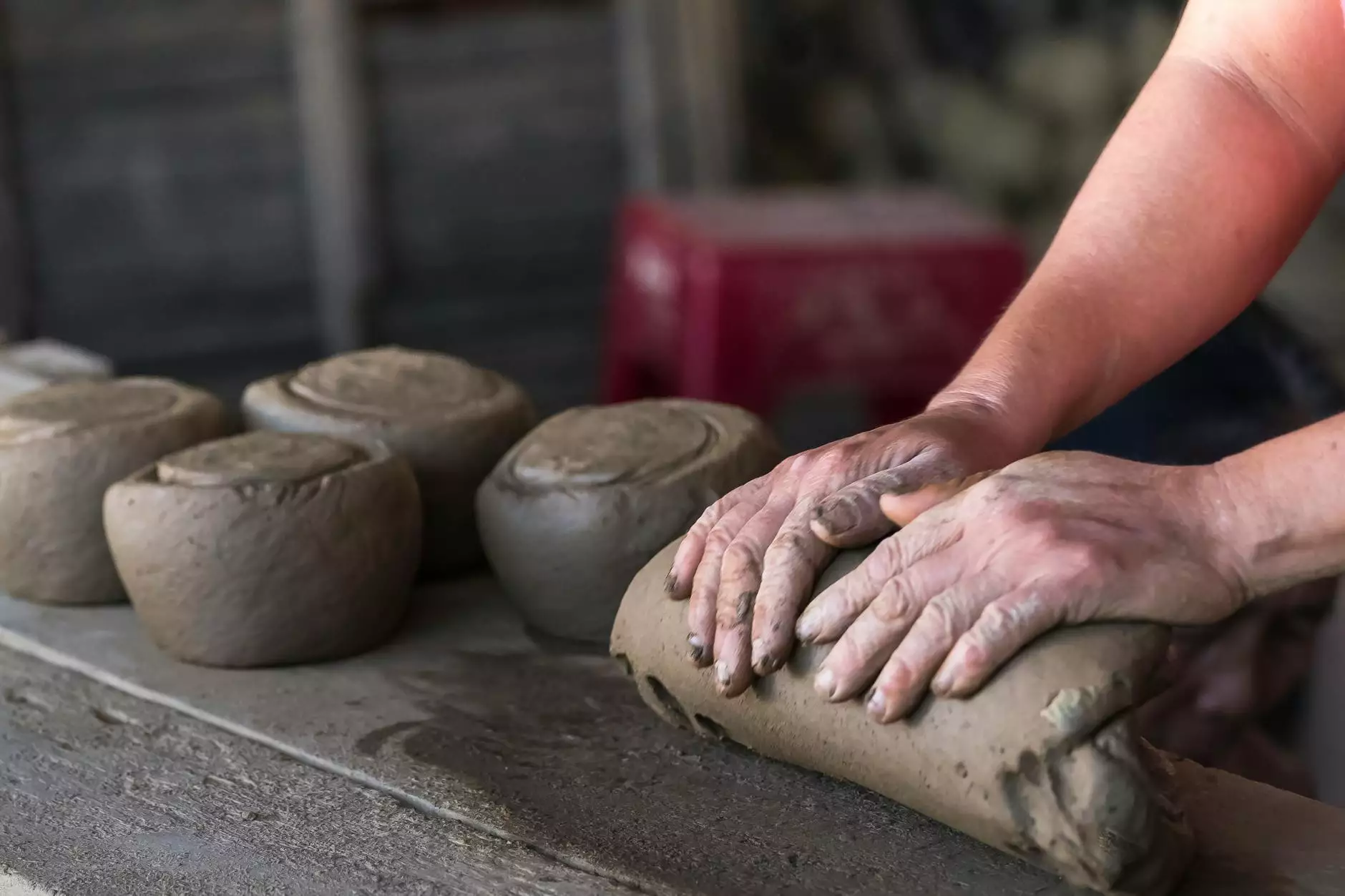
Injection molding manufacturing is an essential process in the realm of industrial production, playing a crucial role in creating a diverse range of plastic products. This article aims to delve deep into the intricacies of injection molding, explore its applications, and highlight its importance within the manufacturing industry, particularly for businesses like Deepmould.net that specialize in this domain.
What is Injection Molding?
Injection molding is a manufacturing process where molten material, typically plastic or metal, is injected into a mold to create specific shapes and designs. This method is highly efficient for mass production, making it a preferred choice for various industries. The primary materials used in injection molding include:
- Thermoplastics: These are the most common materials used in injection molding, as they can be heated and cooled repeatedly without causing damage.
- Thermosetting plastics: Unlike thermoplastics, these materials undergo a chemical change when heated, making them irreversible.
- Metals: Certain metal injection molding processes allow for the creation of complex metal parts, combining the benefits of molding with the durability of metals.
The Injection Molding Process
The process of injection molding manufacturing consists of several stages, each critical to ensuring the quality and precision of the final product. Here’s a detailed breakdown of the steps involved:
- Mold Design: A well-designed mold is the foundation of successful injection molding. The design must account for factors such as part complexity, material selection, and cooling requirements.
- Material Selection: Choosing the right material is vital. Factors like strength, flexibility, and temperature resistance play significant roles in deciding which plastic or metal to use.
- Heating: The raw material is heated until it reaches a molten state, allowing it to flow easily into the mold.
- Injection: The molten material is injected into the mold under high pressure, filling every detail and cavity to ensure an accurate replication of the desired shape.
- Cooling: After injection, the material is allowed to cool and solidify. This stage is critical, as improper cooling can lead to defects.
- Mold Removal: Once solidified, the mold opens to extract the finished product. This step must be handled with care to avoid damaging the part.
- Finishing: Depending on the requirements, additional processes such as trimming, painting, or assembly may take place to achieve the final product.
Benefits of Injection Molding Manufacturing
Injection molding offers numerous advantages that make it an attractive option for manufacturers. Some key benefits include:
- High Efficiency: Once the mold is created, the production cycle can be very rapid, often yielding thousands of parts in a single day.
- Precision: Injection molding allows for high levels of precision in producing complex shapes and intricate details, which is crucial in industries like automotive and medical devices.
- Material Versatility: A wide variety of materials can be used, making injection molding suitable for many applications.
- Reduced Waste: This process is highly efficient in material usage, minimizing waste and lowering costs.
- Scalability: Injection molding is optimal for producing large quantities, allowing companies to scale production swiftly as demand increases.
Applications of Injection Molding Manufacturing
Injection molding is utilized across numerous industries, demonstrating its versatility and capability. Some prominent applications include:
1. Automotive Industry
The automotive sector extensively employs injection molding to manufacture various components, from dashboards to door panels. Injection molded parts contribute to lighter and more fuel-efficient vehicles.
2. Medical Devices
In the healthcare industry, precision and sterility are essential. Injection molding produces medical devices, laboratory equipment, and packaging that meet stringent standards.
3. Consumer Goods
From household items to electronics, many consumer goods are manufactured using injection molding. This process enables the creation of aesthetically pleasing and functional products at scale.
4. Industrial Machinery
Injection molding is also used to create durable components for industrial machinery, offering strength and resilience needed for operation.
Challenges in Injection Molding Manufacturing
While injection molding has many advantages, it also comes with challenges that manufacturers must navigate:
- Mold Design Complexity: Creating an effective mold can be costly and time-consuming, often requiring significant expertise.
- Material Limitations: Not all materials are suitable for injection molding, and selecting the wrong type can result in product failure.
- Initial Investment: The upfront costs for machinery and mold creation can be high, posing a barrier for smaller businesses.
Future Trends in Injection Molding Manufacturing
As technology advances, injection molding manufacturing continues to evolve. Here are some emerging trends to watch:
1. Additive Manufacturing Integration
The combination of injection molding with additive manufacturing techniques provides opportunities for custom mold designs, improving efficiency and reducing waste.
2. Sustainable Practices
With growing environmental concerns, the industry is moving towards eco-friendly materials and processes, emphasizing recycling and reduced energy consumption.
3. Smart Manufacturing
The integration of IoT and automation technologies is expected to boost efficiency, predictive maintenance, and overall production quality in injection molding.
Why Choose Deepmould.net for Injection Molding Manufacturing
When considering an injection molding partner, Deepmould.net stands out for several reasons:
- Expertise: With years of experience in the industry, Deepmould.net offers unparalleled knowledge and skills in injection molding.
- Advanced Technology: Utilizing the latest technologies ensures high precision, efficiency, and quality in every part produced.
- Customization: We understand that every client has unique needs, and we pride ourselves on providing tailored solutions for all injection molding projects.
- Commitment to Sustainability: Deepmould.net is dedicated to environmentally friendly practices, ensuring that our operations are sustainable.
Conclusion
In conclusion, injection molding manufacturing plays a pivotal role in modern production across various industries. Its efficiency, precision, and ability to produce complex parts make it an invaluable process for manufacturers. As these techniques continue to evolve with technological advancements, companies such as Deepmould.net are poised to lead the way in innovative solutions. By understanding the benefits, applications, and future trends of injection molding, businesses can harness its full potential to drive growth and improve their product offerings.