The Exponential Growth of Plastics Molding in Modern Manufacturing
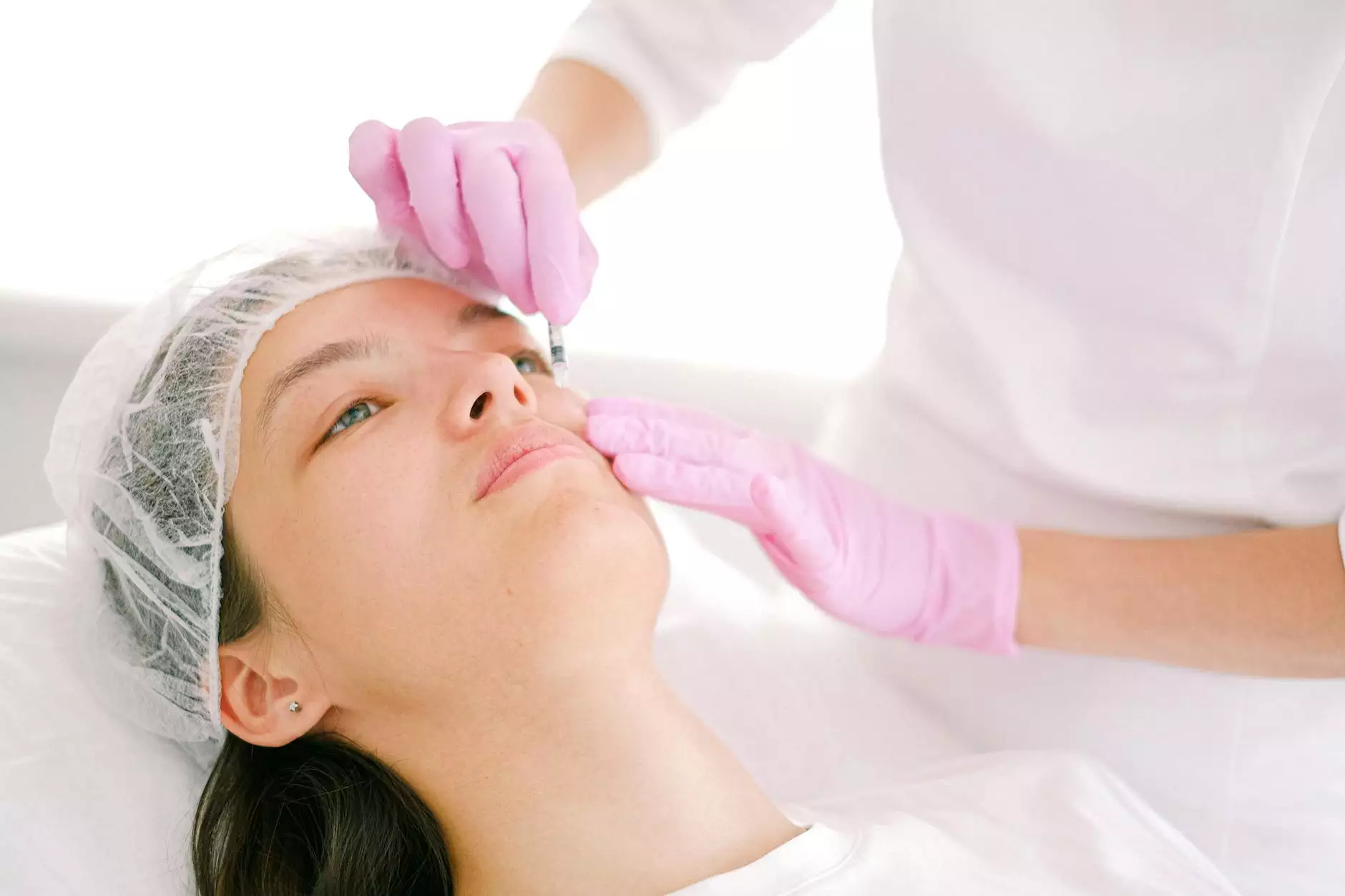
In recent years, the manufacturing sector has seen a remarkable transformation, largely attributable to the advancements in plastics molding. As companies seek more efficient and cost-effective production methods, the realm of plastics molding has emerged as a pivotal solution. This article delves deep into the world of plastics molding, examining its processes, advantages, and the myriad ways it revolutionizes business practices.
Understanding Plastics Molding
Plastics molding is a manufacturing process used to create parts by shaping liquid plastic into a mold. This technique is essential in producing a range of products, from simple household items to complex components used in various industries. The fundamental processes involved in plastics molding include:
- Injection Molding: This involves injecting molten plastic into a mold cavity, allowing the material to cool and solidify into the desired shape.
- Blow Molding: This method shapes hollow plastic parts by blowing air into a molten plastic tube, forming a bubble that takes the shape of the mold.
- Rotational Molding: In this process, powdered plastic is placed in a mold and rotated to evenly coat the interior, creating hollow parts.
- Compression Molding: This involves placing a plastic material into an open mold, which is then closed to apply pressure and heat, shaping the material into the desired form.
The Advantages of Plastics Molding
The benefits of adopting plastics molding in manufacturing can’t be overstated. Here are key advantages that businesses can leverage:
1. Cost Efficiency
Plastics molding significantly reduces production costs. The efficiency of processes like injection molding allows for high-volume production, which in turn lowers the cost per unit. This is particularly beneficial for businesses operating on tight margins, enabling them to maintain competitiveness in the market.
2. Design Flexibility
One of the standout features of plastics molding is its ability to accommodate complex designs. Modern molding techniques allow for intricate shapes and details, providing designers with greater creative freedom. Custom molds can be developed for specific needs, contributing to enhanced product differentiation.
3. Material Variety
With a vast array of plastic materials available, from polycarbonate to polypropylene, manufacturers can select the most suitable option for their applications. This diversity allows for the creation of products with varying properties, such as flexibility, strength, and resistance to chemicals.
4. Reduced Waste
Efficient molding processes minimize material waste compared to traditional manufacturing methods. Techniques like injection molding generate less scrap, making it an environmentally friendly choice. Additionally, companies can implement recycling procedures for sustainable practices.
5. Speed of Production
The speed at which products can be produced with plastics molding is another key advantage. Rapid prototyping can drastically shorten product development timelines, allowing businesses to respond swiftly to market demands.
Applications of Plastics Molding Across Industries
Plastics molding finds application in various sectors, showcasing its versatility and crucial role in modern manufacturing. Here are some prominent industries benefiting from this technology:
1. Automotive Industry
The automotive sector utilizes plastics molding extensively for producing components such as dashboards, bumpers, and interior parts. These molded parts are lightweight yet durable, contributing to fuel efficiency and overall vehicle performance.
2. Consumer Goods
Everyday products, from toys to kitchenware, rely on plastics molding. The ability to produce high-quality, aesthetically pleasing products makes it ideal for the consumer goods market. Companies can also produce custom packaging solutions that enhance product appeal.
3. Medical Devices
In the healthcare field, plastics molding is integral for manufacturing critical medical devices. Items such as syringes, IV bags, and surgical instruments are produced with high precision and stringent sanitary standards, ensuring safety and efficacy.
4. Electronics
Electronics manufacturers leverage molding techniques to produce components that require precision and reliability. From casings to connectors, molded plastics play a vital role in the functionality of electronic devices.
5. Aerospace
The aerospace industry benefits from lightweight plastic parts that do not compromise strength or safety. Plastics molding allows for the production of components that contribute to fuel efficiency and lower overall weight, enhancing aircraft performance.
Innovations in Plastics Molding
The landscape of plastics molding is continuously evolving, thanks to ongoing technological advancements. Here are some innovations currently shaping the industry:
1. 3D Printing and Molding
Integrating 3D printing with traditional molding processes allows for rapid prototyping and complex designs. This hybrid approach enables manufacturers to create unique molds more quickly and at lower costs.
2. Smart Plastics
Innovations in material science have led to the development of smart plastics with properties that can change in response to environmental stimuli. These materials open doors to new applications across various industries where adaptability is key.
3. Sustainable Practices
With a growing emphasis on sustainability, many companies are exploring eco-friendly materials for plastics molding. Biodegradable plastics and recycling processes are gaining traction, promoting responsible production practices.
The Future of Plastics Molding
As industries continue to innovate, the future of plastics molding looks promising. Key trends driving the evolution of this sector include:
- Increased Automation: With advancements in robotics and machine learning, automation is expected to streamline production processes further, improving speed and precision.
- Circular Economy Initiatives: As companies focus on reducing waste, processes that enable recycled materials to be used effectively in molding are likely to expand.
- Research and Development: Ongoing R&D efforts aim to enhance the performance of plastics, leading to new applications and improved product properties.
- Global Expansion: As markets grow, the demand for molded plastics in emerging economies is anticipated to rise, fostering new business opportunities.
Conclusion
The realm of plastics molding represents a dynamic and essential facet of modern manufacturing. By embracing the efficiencies, design possibilities, and cost benefits associated with this technology, businesses can position themselves for success in an intensely competitive landscape. It is imperative for companies, particularly in sectors like automotive, consumer goods, and electronics, to leverage plastics molding as a strategic advantage. As innovation continues to drive this industry forward, those who can adapt and evolve will undoubtedly thrive in the ever-changing marketplace.
To explore how Deep Mould can assist your business with high-quality plastics molding solutions, visit deepmould.net for more information.