Precision Injection Molds: Revolutionizing Metal Fabrication
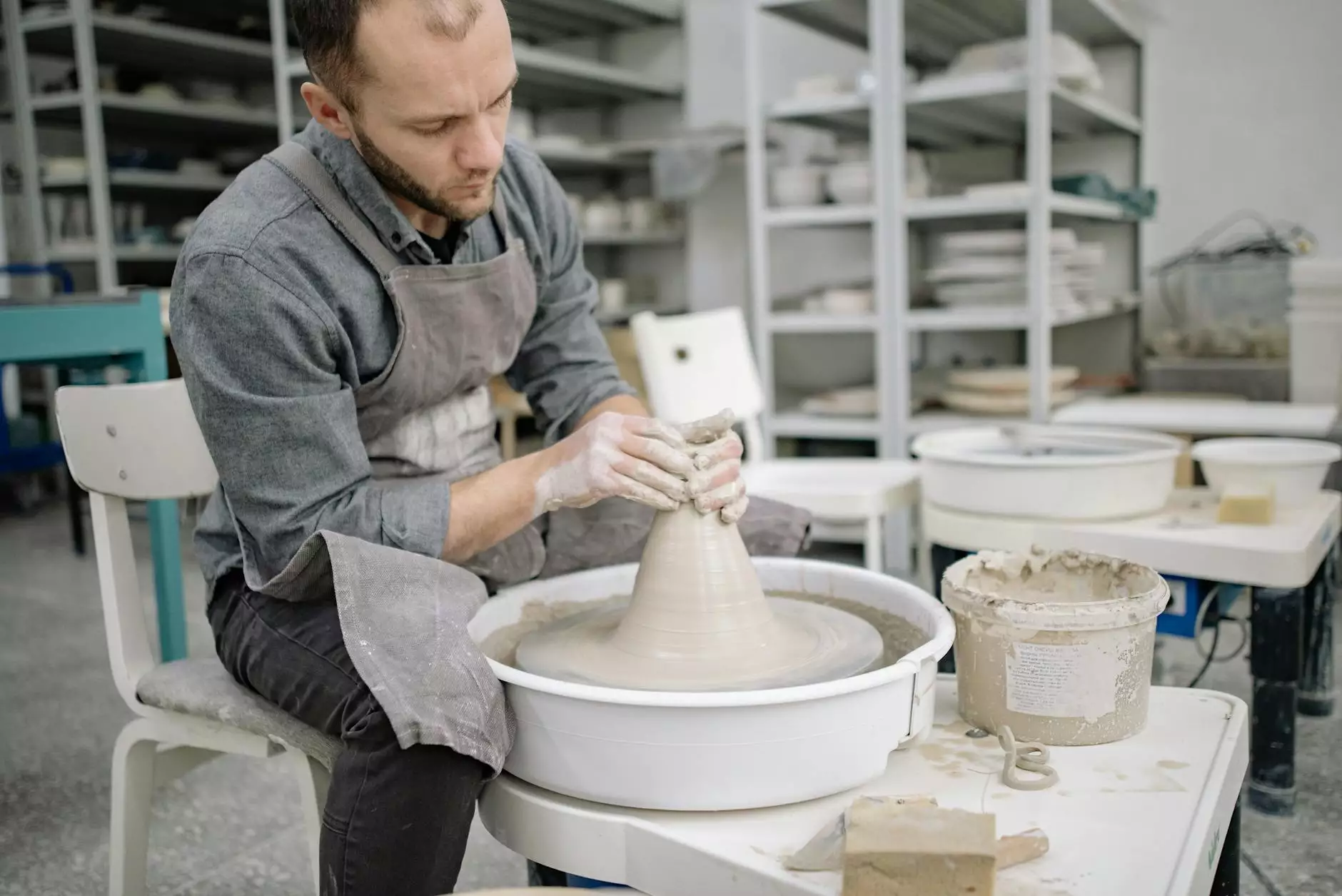
In the rapidly evolving landscape of manufacturing, precision injection molds are becoming increasingly vital. These molds are at the forefront of innovation, facilitating the production of intricate components that meet the strictest tolerances.
The Importance of Precision Injection Molds in Metal Fabrication
The role of precision injection molds in the metal fabrication industry cannot be overstated. They are essential for producing high-quality products with exceptional accuracy. Understanding their significance provides insights into how they enhance manufacturing processes.
Why Precision Matters
In any manufacturing setup, precision is crucial. In metal fabrication, even the smallest imperfection can lead to operational failures or economic losses. Precision injection molds ensure that components are crafted with exactness, which translates into:
- Improved Product Quality: Items produced utilizing these molds exhibit superior finish and consistency.
- Enhanced Efficiency: The accuracy of the molds minimizes waste and reduces the time taken in the manufacturing process.
- Cost-Effectiveness: By minimizing defects, companies save money on rework and material costs.
Applications of Precision Injection Molds
Precision injection molds are utilized across various industries, showcasing their versatility. Some notable applications include:
1. Automotive Industry
The automotive sector relies heavily on precision injection molds to fabricate components such as:
- Dashboard elements
- Housings for electronic components
- Interior and exterior trim pieces
These molds ensure that parts meet stringent safety and performance standards.
2. Consumer Electronics
Consumer electronics require intricate designs and tight tolerances. Molds for:
- Smartphone casings
- Battery covers
- Plug and connector housings
are ideally created using precision injection molds, allowing manufacturers to deliver aesthetically pleasing, functional products.
3. Medical Devices
The medical field demands components that not only exhibit precision but are also manufactured under strict regulatory standards. Examples include:
- Syringes
- Implants
- Diagnostic equipment
Utilizing precision molds ensures these items are reliable and safe for patient use.
The Manufacturing Process of Precision Injection Molds
Understanding the manufacturing process of precision injection molds is essential for businesses looking to implement these technologies. Here’s a breakdown of the steps involved:
1. Design and Prototyping
The first step in creating a precision injection mold is the design phase. Utilizing advanced software like CAD (Computer-Aided Design), engineers create detailed designs that enhance mold efficiency. Prototyping allows for testing and modification before mass production.
2. Material Selection
Choosing the right materials for the mold is critical. Common materials include:
- Steel: Offers durability and longevity.
- Aluminum: Provides lightweight options with a faster turnaround time.
The selected material impacts the mold’s performance and the quality of the final product.
3. Machining and Manufacturing
Once the design and materials are finalized, advanced machining techniques, such as EDM (Electrical Discharge Machining) and CNC (Computer Numerical Control) milling, are employed. These techniques allow for the intricate designs required in the molds.
4. Assembly and Testing
After manufacturing individual parts, they are assembled into the final mold. Rigorous testing follows to ensure that the molds perform as expected, maintaining the necessary precision throughout the production lifecycle.
The Advantages of Using Precision Injection Molds
Businesses stand to gain numerous benefits from integrating precision injection molds into their manufacturing processes:
1. Scalability
Precision molds allow for relatively quick transition from prototypes to mass production, making it easier for companies to scale their operations without compromising on quality.
2. Customization
With the aid of advanced design software, manufacturers can easily modify molds to suit different products. This flexibility encourages innovation and caters to diverse client needs.
3. Reduced Labor Costs
Automated systems are often used in conjunction with injection molding, leading to lower labor costs as fewer workers are needed to manage the production process.
Challenges Faced by the Precision Injection Molding Industry
While the benefits are substantial, the industry does face certain challenges:
1. Initial Investment
The setup costs for precision injection molds can be high, deterring smaller businesses from entering the market.
2. Maintenance and Repair
Maintaining precision molds requires regular inspections and, at times, repairs. This maintenance can lead to increased downtime if not managed effectively.
3. Technical Expertise
Operating precision injection molding machines requires skilled personnel. The shortage of trained professionals can hinder production capabilities for some companies.
Future Trends in Precision Injection Molding
The future of precision injection molds is promising, with advancements shaping the industry profoundly. Some trends to watch include:
1. Automation and Smart Manufacturing
As factories adopt Industry 4.0 principles, automation is becoming more prevalent. Smart sensors and AI technology are set to streamline the injection molding process, further enhancing precision and efficiency.
2. Sustainable Practices
Businesses are increasingly focused on sustainability. The development of molds that reduce material waste and energy consumption is a growing trend, appealing to environmentally conscious consumers.
3. Advances in Materials
Innovations in polymer science are leading to the creation of new materials that are lighter, stronger, and more durable. These materials enhance the capabilities of precision injection molds significantly.
Conclusion
As detailed, precision injection molds play an integral role in transforming the metal fabrication industry. From the automotive sector to medical devices, these molds provide unparalleled quality, efficiency, and customization capabilities. While challenges exist, the future holds exciting possibilities, ensuring that precision injection molding continues to thrive and drive business innovation.
For companies looking to leverage the power of precision injection molds, the time to invest in these technologies is now. Engage with skilled experts and embrace new trends to stay ahead in the competitive landscape.
For more information, visit DeepMould.net.